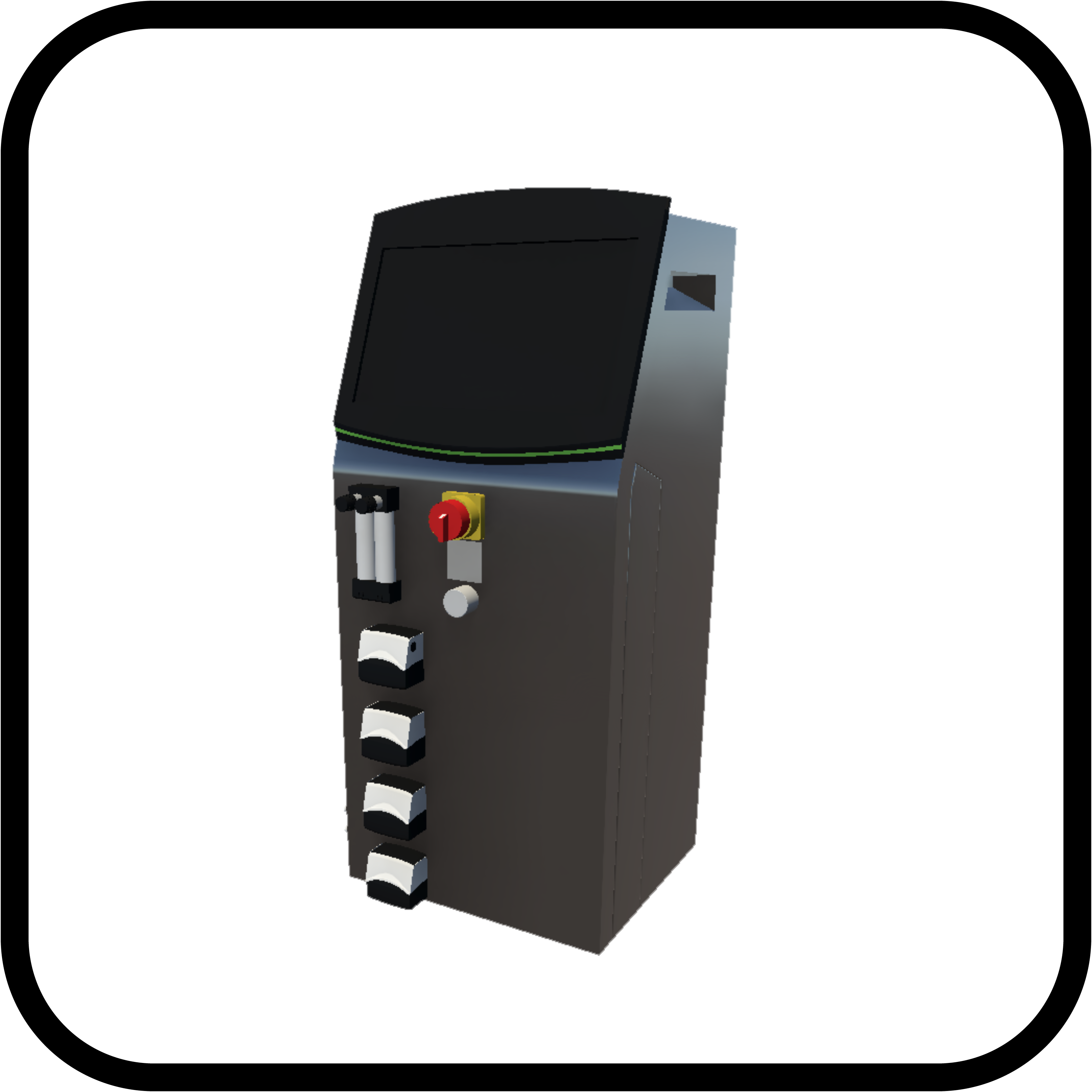
BIOREACTOR CONTROLLER
生物反应器控制器是一种重要的生物制造仪器,可调节温度、pH 值和搅拌速度,以实现最佳细胞培养。作为生物加工的关键,它可确保生物产品的完整性、无菌性和安全性。它是治疗和诊断的理想选择,是可靠的守护者,有助于在生物技术中获得一致、无污染的结果。 View All Equipment.
设置
The setup of a bioreactor controller involves several steps and components. Here is a general overview of the setup process:
Unboxing and Inspection: Carefully unpack the bioreactor controller and inspect all components for any signs of damage incurred during shipping.
Read the User Manual: Thoroughly read the user manual provided by the manufacturer to understand the specifications, features, and safety guidelines.
Power Connection: Connect the bioreactor controller to a stable and appropriate power source using the supplied power cable.
Peripheral Connections: Connect any peripheral devices, such as sensors, actuators, and pumps, according to the manufacturer’s guidelines.
Communication Interfaces: Set up communication interfaces, such as USB, Ethernet, or any other specified by the manufacturer, to enable data exchange with external systems.
Control Software Installation: Install the required control software on a compatible computer or system. Follow the installation instructions provided by the manufacturer.
Calibration of Sensors: Calibrate all sensors connected to the bioreactor controller following the calibration procedures outlined in the user manual.
Configuration of Setpoints: Configure the desired operating parameters, including temperature, pH, dissolved oxygen levels, and any other relevant setpoints.
Alarm Settings: Set up alarm thresholds for critical parameters to ensure timely detection and response to deviations during operation.
User Authentication: If applicable, set up user authentication features to control access to the bioreactor controller and its settings.
Data Logging Configuration: Configure data logging parameters to record and store relevant process data for analysis and documentation.
Integration with SCADA or DCS Systems: If applicable, integrate the bioreactor controller with Supervisory Control and Data Acquisition (SCADA) or Distributed Control System (DCS) for centralized monitoring and control.
Testing and Validation: Conduct initial tests to validate the functionality of the bioreactor controller. Ensure that sensors, actuators, and software interfaces work as intended.
System Interlock Checks: Verify interlock systems to ensure that safety features are functioning correctly and can shut down the system in case of emergencies.
Training for Operators: Provide training to operators on the proper use of the bioreactor controller, including navigating the user interface, responding to alarms, and performing routine maintenance.
Documentation: Maintain detailed documentation of the setup process, including calibration records, configuration settings, and any modifications made.
Emergency Procedures: Establish and communicate emergency procedures to operators, detailing the steps to be taken in case of system malfunctions or safety concerns.
Regular Maintenance Schedule: Develop and implement a regular maintenance schedule for the bioreactor controller, including sensor recalibration, software updates, and hardware checks.
Compliance with Regulations: Ensure that the setup and operation of the bioreactor controller comply with relevant industry standards and regulations.
Continuous Monitoring: Continuously monitor the bioreactor controller during initial runs to identify any issues and make necessary adjustments.
Feedback to Manufacturer: Provide feedback to the manufacturer regarding any observations, issues, or recommendations for improvement during the setup and initial operation.
Recordkeeping: Maintain a comprehensive record of system performance, alarms, and any troubleshooting steps taken for future reference.
Recordkeeping: Maintain a comprehensive record of system performance, alarms, and any troubleshooting steps taken for future reference.
Please note that this is a general outline, and the specific steps and procedures for setting up a bioreactor controller may vary depending on the manufacturer, model, and application. Always consult the manufacturer’s guidelines and any applicable safety procedures before attempting to set up and operate it.
错误代码
Bioreactor Controllers can experience various error conditions during operation, which may affect the efficiency and quality of the biological process. Some common error conditions include:
Power Supply Issues: Sudden power outage affecting the bioreactor controller, leading to a loss of control and potential data corruption. Fluctuations in power supply causing instability in the controller’s operation.
Sensor Malfunction: Failure or drift in readings from critical sensors (e.g., pH, temperature, dissolved oxygen), leading to inaccurate process monitoring and control. Complete sensor failure resulting in a lack of real-time data.
Communication Failure: Loss of communication with peripheral devices such as pumps, actuators, or sensors, disrupting the coordinated functioning of the bioreactor system. Failure in data transmission to external monitoring or control systems.
Control Software Crash: Unexpected crashes or freezes in the control software, hindering the ability to adjust parameters and respond to changing conditions. Software bugs causing erratic behavior in the control algorithms.
Alarm System Failure: Inability of the alarm system to detect critical deviations or malfunctions in the bioreactor system. Frequent false alarms or failure to trigger alarms during actual issues.
Temperature Control Issues: Inability to maintain set temperatures, leading to thermal stress on the culture. Fluctuations in temperature control impacting cell viability and growth.
Pump or Actuator Failures: Failure of pumps or actuators responsible for media feeding, leading to disruptions in nutrient supply. Stuck or unresponsive actuators affecting fluid flow dynamics.
Data Logging Problems: Failure in recording or storing process data, resulting in a loss of historical information for analysis. Corrupted data logs compromising the traceability of process events.
User Authentication Issues: Problems with user authentication systems, potentially allowing unauthorized access to the controller. Inability to properly authenticate and assign user privileges.
Integrative System Failures: Breakdown in the integration between the bioreactor controller and higher-level systems such as SCADA or DCS. Loss of centralized monitoring and control capabilities.
Mechanical Failures: Physical malfunctions in the controller hardware, such as buttons, knobs, or touchscreen, hindering user interaction. Structural issues affecting the overall integrity of the controller.
Network Security Breach: Unauthorized access to the bioreactor controller through network vulnerabilities. Compromised data integrity due to security breaches.
Fluid Leakage: Leakage of process fluids from the controller, potentially leading to contamination or damage to surrounding equipment.
Emergency Shutdown Failure: Inability to execute an emergency shutdown in response to critical failures or safety concerns. Failure of safety interlock systems to halt operations during emergencies.
Software Incompatibility: Compatibility issues between the bioreactor controller software and connected devices or systems. Unexpected interactions with other software running on the same platform.
Inadequate Backup Systems: Failure of backup systems to take over in the event of a primary system failure. Insufficient redundancy measures leading to a single point of failure.
Calibration Drift: Drift in sensor calibration over time, leading to inaccuracies in measurement and control. Lack of regular calibration resulting in degraded performance.
High Noise in Sensor Signals:Excessive noise or interference in sensor signals, affecting the accuracy of measurements. Difficulty distinguishing valid readings from noise.
Inadequate Emergency Response:Lack of proper response to critical conditions, such as failure to activate safety features during emergencies. Delayed or inadequate response to alarms or deviations.
Unintended Parameter Changes:Unintended changes in control parameters, potentially resulting from software bugs or user errors. Incorrectly adjusted setpoints impacting the overall process.
These error conditions highlight various potential issues that may arise in a bioreactor controller system, impacting its reliability, accuracy, and safety.