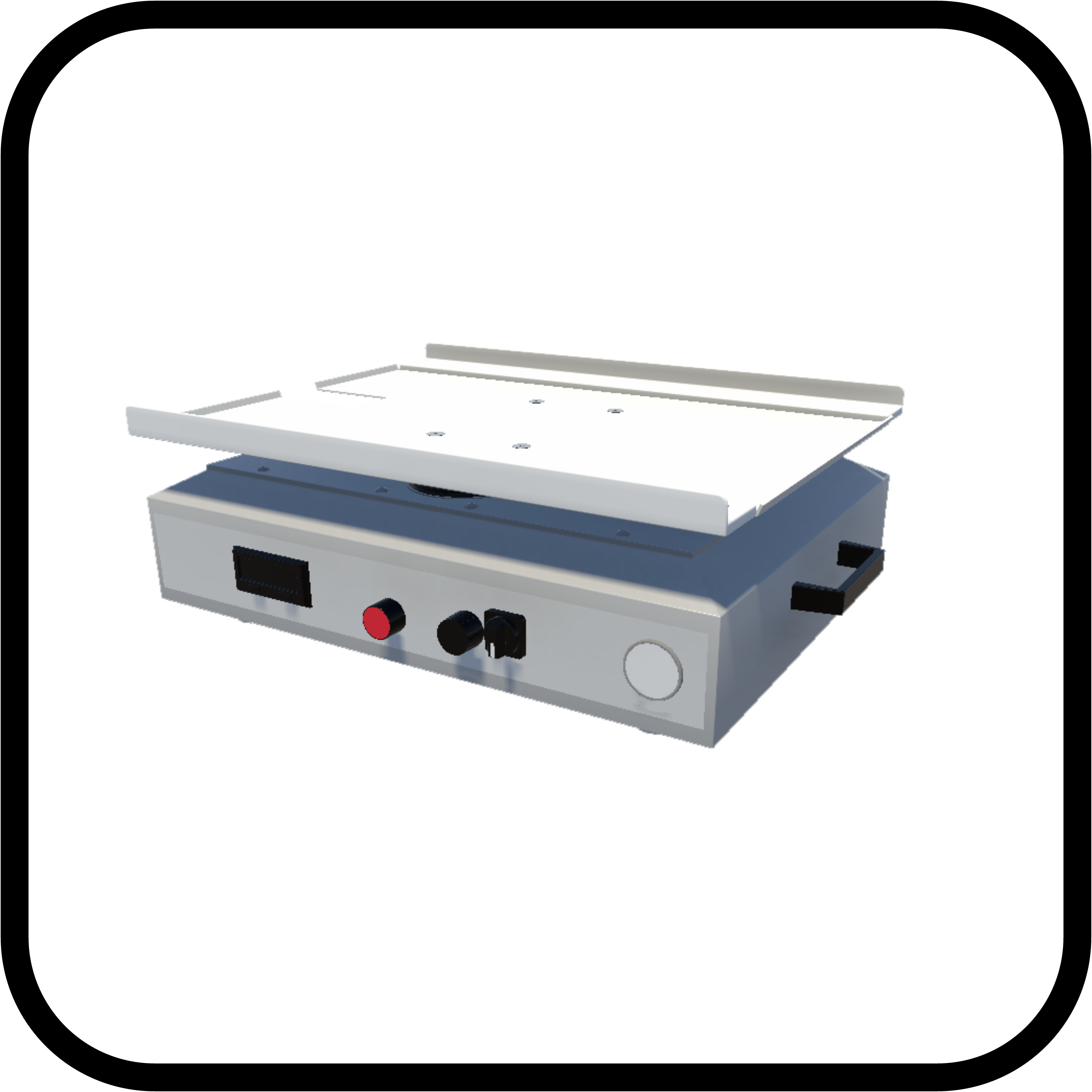
WAVE BIOREACTOR
A Wave Bioreactor is a revolutionary system in biomanufacturing, introducing a novel approach to cell culture. Utilizing rocking motion technology, it provides efficient and scalable processes for the production of biological products. With its wave-like motion, it optimizes oxygen and nutrient transfer, enhancing cell growth. This innovative bioreactor is ideal for applications in pharmaceuticals, biopharmaceuticals, and biofuel development, offering a dynamic and controlled environment for robust cell cultivation. View All Equipment.
SETUP
The setup of a wave bioreactor involves several steps and components. Here is a general overview of the setup process:
Location and Environment: Choose a suitable location with adequate space and proper environmental conditions. Ensure proper ventilation and access to utilities (electricity, water, and gas).
Inspect Equipment: Carefully inspect the wave bioreactor components for any damage incurred during transportation. Verify that all components are present as per the equipment checklist.
Prepare Work Area: Clean the work area to maintain a sterile environment. Wear appropriate personal protective equipment (PPE) to prevent contamination.
Assemble the Wave Bioreactor System: Follow the manufacturer’s instructions to assemble the wave bioreactor system. Connect tubes, sensors, and other components according to the provided schematics.
Prepare the Bioreactor Bag: Ensure the integrity of the bioreactor bag. – Connect the bag to the wave bioreactor system, securing all connections. Perform necessary leak tests.
Sterilization: Sterilize the entire wave bioreactor system using the recommended method (e.g., autoclaving or gamma irradiation). Follow the manufacturer’s guidelines for sterilization time and conditions.
Media and Buffer Preparation: Prepare cell culture media and buffers according to established protocols. Sterilize the media using appropriate methods.
Calibrate Sensors: Calibrate sensors such as pH, dissolved oxygen, and temperature based on the manufacturer’s specifications. Ensure proper functioning of all sensors.
Inoculation and Seeding: Inoculate the wave bioreactor with the desired cells or microorganisms. Follow recommended seeding density and inoculation procedures.
Set Operating Parameters: Input desired process parameters, including temperature, pH setpoints, agitation speed, and aeration rate. Configure the control system according to your specific process requirements.
Monitor and Control: Monitor the wave bioreactor system throughout the culture process. Adjust control parameters based on sensor readings.
Harvesting: Follow appropriate procedures for harvesting cells or microorganisms when the culture reaches the desired state.
Dispose of Single-Use Components: Dispose of the bioreactor bag and other single-use components in accordance with local regulations.
Documentation: Maintain detailed records of the entire setup process, including sterilization, inoculation, and process parameters.
Cleaning and Storage: Clean the wave bioreactor system after use according to the manufacturer’s guidelines. Store components properly for future use.
Training and Familiarization: Ensure that operators are trained on the proper use and maintenance of the wave bioreactor system. Familiarize personnel with emergency procedures and troubleshooting techniques.
Validation and Qualification: Perform validation and qualification activities as required by regulatory standards. Ensure that the wave bioreactor system meets specified performance criteria.
Emergency Preparedness: Establish procedures for responding to emergencies or unexpected events during bioreactor operation. Keep emergency contact information readily available.
Regular Maintenance: Implement a schedule for routine maintenance tasks, including sensor calibration and system checks. Follow the manufacturer’s recommendations for maintenance intervals.
Continuous Improvement: Periodically review and update standard operating procedures based on experience and lessons learned. Stay informed about updates or improvements provided by the manufacturer.
Training and Recordkeeping: Provide ongoing training for operators to stay current with best practices. Maintain accurate and up-to-date records of bioreactor usage, maintenance, and performance.
Please note that this is a general outline, and the specific steps and procedures for setting up a wave bioreactor may vary depending on the manufacturer, model, and application. Always consult the manufacturer’s guidelines and any applicable safety procedures before attempting to set up and operate a bioreactor.
ERROR CODES
Wave Bioreactors can experience various error conditions during operation, which may affect the efficiency and quality of the biological process. Some common error conditions include:
Power Supply Issues: Unexpected power outage affecting the operation of the wave bioreactor. Voltage fluctuations leading to disruptions in the power source.
Agitation System Failures: Malfunction of the agitation system, causing irregular or insufficient mixing. Agitation motor or paddle issues impacting overall performance.
Temperature Control Problems: Inability to maintain set temperatures for the culture. Overheating or undercooling of the bioreactor environment.
Sensor Malfunction: Faulty readings from critical sensors such as pH, dissolved oxygen, or temperature. Sensor drift affecting the accuracy of process control.
Leaks and Contamination: Fluid leaks from the bioreactor, compromising the sterility of the culture. Contamination issues affecting the quality of the cell culture.
Pump System Failures: Failure of the pump system, leading to disruptions in media or nutrient delivery. Pump motor or tubing issues impacting fluid dynamics.
Foam formation: Excessive foam generation during agitation, causing potential overflow or contamination. Inadequate foam control mechanisms.
Air Supply Issues: Insufficient or disrupted air supply affecting aeration and gas exchange. Airflow blockages or issues with the sparging system.
pH Drift: Unintended fluctuations in pH levels, impacting the cellular environment. Inability to maintain the desired pH setpoints.
Communication Failures: Issues with communication between the control system and peripheral devices. Failure of data logging or recording mechanisms.
Harvesting Problems: Difficulties in initiating or completing the harvesting process. Issues with the harvest pump or associated components.
Alarms and Alerts: Ignoring or failure to address system alarms and alerts promptly. Frequent triggering of alarms without resolution.
Bioreactor Bag Integrity: Compromised integrity of the single-use bioreactor bag. Leaks, tears, or other issues with the bag material.
Mechanical Failures: Structural or mechanical failures in the wave bioreactor system. Issues with moving parts, such as the rocking mechanism.
Control System Malfunction: Failure of the control panel or software, impacting process parameter adjustments. Inability to input or modify operating parameters.
Harvesting Pump Failure: Malfunction or failure of the pump used for harvesting cells or culture. Issues with tubing, valves, or other components in the harvesting system.
Foam Control Device Failure: Malfunction of devices designed to control foam during agitation. Inadequate foam control leading to operational issues.
Inoculation Problems: Difficulties in initiating the inoculation process. Issues with the inoculation pump or related components.
Sterility Compromises: Events or conditions leading to compromised sterility within the bioreactor. Contamination events impacting the entire culture.
Oxygen Supply Issues: Insufficient oxygen supply affecting cell viability and growth. Problems with the oxygenation system or sparging.
To minimize the occurrence of error conditions, it is essential to follow proper operating procedures, implement preventive maintenance schedules, and closely monitor the bioprocess parameters throughout the operation.